新書推薦:
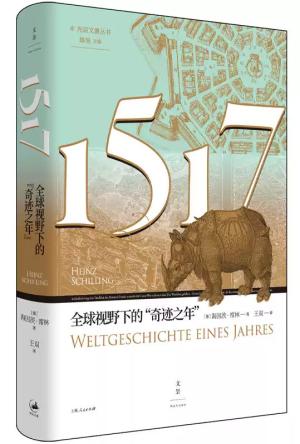
《
1517:全球视野下的“奇迹之年”
》
售價:NT$
449.0
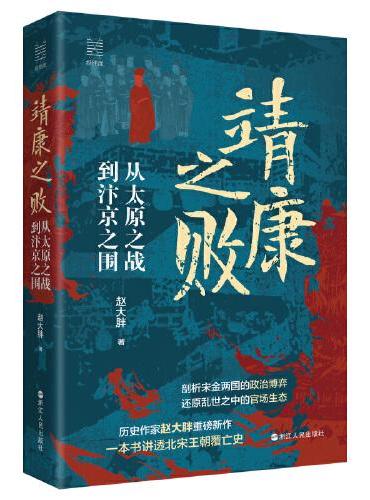
《
经纬度丛书·靖康之败:从太原之战到汴京之围
》
售價:NT$
398.0
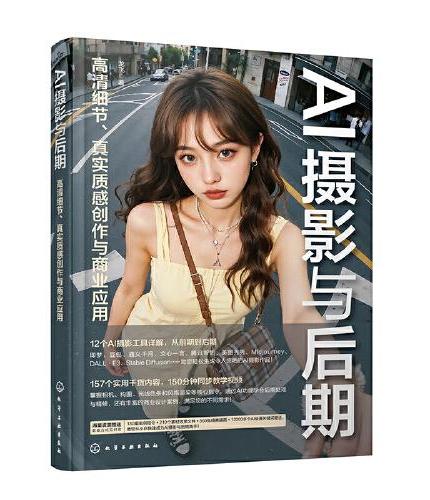
《
AI摄影与后期:高清细节、真实质感创作与商业应用
》
售價:NT$
500.0
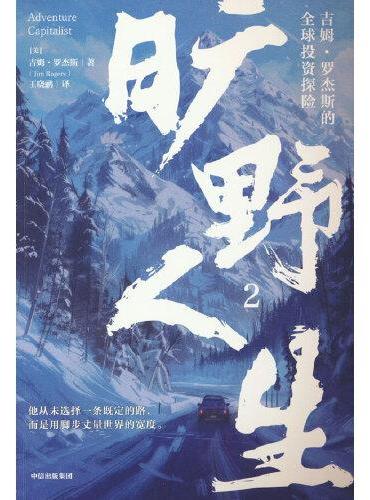
《
旷野人生2:吉姆·罗杰斯的全球投资探险
》
售價:NT$
352.0
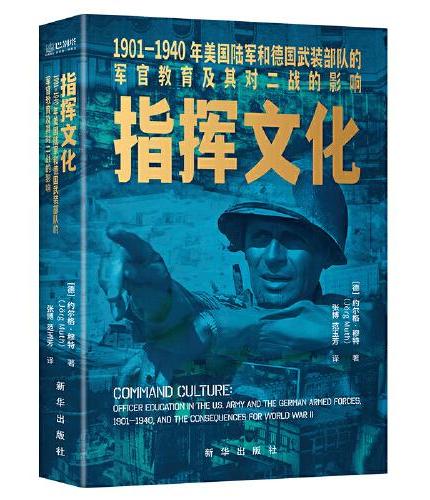
《
指挥文化: 1901—1940 年美国陆军和德国武装部队的军官教育及其对二战的影响
》
售價:NT$
398.0

《
为了治愈:改变医学的 30 个诺贝尔奖
》
售價:NT$
301.0
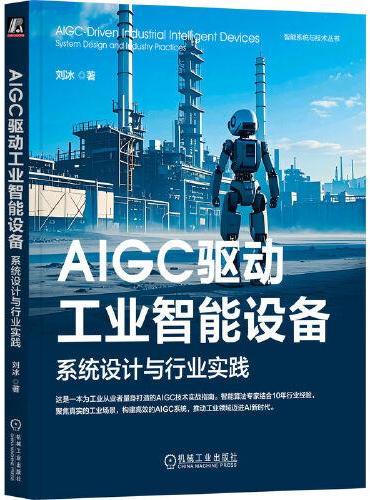
《
AIGC驱动工业智能设备:系统设计与行业实践
》
售價:NT$
505.0
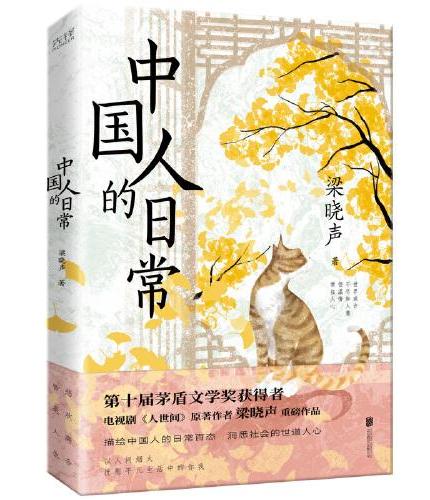
《
中国人的日常(茅盾文学奖获得者、《人世间》原著作者梁晓声文集,描绘中国人的日常百态,洞悉社会的世道人心)
》
售價:NT$
301.0
|
內容簡介: |
第五版FMEA基本上对整个FMEA都进行了修改,一些专业术语的定义进行了更新,比如失效模式、失效效应。 何时要采取纠正措施重新进行了定义。
本书对DFMEA和产品图、产品规格书、包装规范的逻辑关系,PFMEA和工艺流程图、控制计划、作业指导书的逻辑关系进行了详细讲解,只有知道了他们的先后顺序及逻辑关系,才能灵活运用。
本书针对DFMEA和PFMEA制作的步骤,通过案例进行了详细解释,读者只要按老师提供的步骤进行制作FMEA就可。FMEA是一个动态过程,而不是一张FMEA表格。
本书针对嵌入式软件进行了FMEA分析也进行了讲解。
本书针对FMEA-MSR监视及系统响应的补充FMEA也是操作步骤及案例。
本书提供了一套全新的程序文件、表格、FMEA表格模板,还有一套考试试题。
|
關於作者: |
谭洪华,江西丰城人,广东中欧企业管理研究所所长,中小企业经营管理咨询专家、国家注册审核员、质量工程师、汽车质量管理体系研究员。中小企业“领导 经营 控制系统”(LBC经营模式)创始人。谭老师先后带领团队辅导过100多家中小企业,给企业带来了不低于30%的有形回报(利润率、成本、执行率、准交率、直通率等指标),同时给管理粗放的中小企业建立了LBM(领导 经营 管理)系统,全面提升了产品品质、准交率、物料损耗率、设备综合性能指数、人均产值、库存周转速度,大大增强了企业的凝聚力、执行力、市场竞争力。
管理没有好坏之分,没有先进不先进之分,只有适合的才是最好的管理。谭老师从基层管理人员出身,做过外资企业的班组长、QC、中高层干部,精通企业管理会计、中国企业文化、各种管理体系认证、日本精益生产模式、美国六西格玛模式,日本阿米巴经营,咨询过程中并能很好的理论与实际相结合,不断总结完善中小企业管理模式,找到了一条适合中国国情的中小企业经营管理之路。
谭老师独创的控制系统与领导系统相适应,经营水平与管理水平相适应,适合中国当下中小企业的实际,推动了企业的快速转型升级,为中小企业经营管理提升做出了杰出贡献。
培训过的企业:
深圳比亚迪汽车、中山TCL、东莞联德电子、惠州至精精密、惠州LG、东莞船井电子、惠州骏亚数字(上市)、河北泰达包装、广东质好建筑模架等行业标杆性企业。
|
目錄:
|
目录
导读
第一篇 FMEA详解
第一章 FMEA的基础知识
一、什么是FMEA
二、FMEA的作用
1.PFMEA的作用
2.DFMEA的作用
3.FMEA-MSR的作用
FMEA作用图
三、谁来做FMEA
四、在什么时候做FMEA
五、DFMEA与PFMEA的不同
六、系统、子系统、部件FMEA的不同
七、FMEA的前提假设
第二章 PFMEA的制作步骤
一、PFMEA规划和准备
1.制作PFMEA工作计划
2.填写PFMEA表头
3.确定边界
二、PFMEA结构分析
1.工艺流程图制作
2.结构树制作
3.FMEA表格结构部分填写
三、PFMEA功能分析
1.功能结构树
2.参数图
FMEA表格功能部分填写
四、PFMEA失效分析
1.失效模式
2.失效影响
3.失效原因
4.一个失效模式导致多个失效影响FE
5.FMEA表格失效分析部分填写
五、PFMEA风险分析
1.当前预防措施PC
2.当前探测措施DC
3.严重度评分S
4.频度评分O
5.探测度评分D
6.措施优先级AP
六、PFMEA工艺优化
1.措施的填写
2.措施的状态
3.有效性跟踪
七、PFMEA标准化
1.把措施移到当前预防和探测
2.制作控制计划
3.制作SOP和SIP
八、PFMEA的动态管理
1.异常和变更
2.谁来主导PFMEA的修正
第三章 DFMEA的制作步骤
一、DFMEA规划和准备
1.制作DFMEA工作计划
2.填写DFMEA表头
3.确定边界
4.DFMEA的前提假设
二、DFMEA结构分析
1.结构树制作
2.边界图制作
3.DFMEA表格结构部分填写
三、DFMEA功能分析
1.功能结构树
2.参数图
3.DFMEA表格功能部分填写
四、DFMEA失效分析
1.失效模式
2.失效影响
3.失效原因
DFMEA表格失效分析部分填写
五、DFMEA风险分析
1.当前预防措施PC
2.当前探测措施DC
3.严重度评分S
4.频度评分O
5.探测度评分D
6.措施优先级AP
六、DFMEA设计优化
1.措施的填写
2.措施的状态
3.有效性跟踪
七、DFMEA标准化
1.把措施移到当前预防和探测
2.制作样品测试计划
八、DFMEA的动态管理
第四章 软件DFMEA的制作步骤
一、软件FMEA概述
1.软件FMEA的分析步骤
2.谁来做软件DFMEA
3.什么时候做软件DFMEA
二、定义软件FMEA分析范围
三、功能矩阵分析
四、软件DFMEA失效分析
五、软件DFMEA风险分析
六、制定纠正措施
七、跟踪改善措施有效性
第五章 FMEA-MSR如何制作
一、FMEA-MSR范围定义
二、FMEA-MSR结构分析
三、FMEA-MSR功能分析
四、FMEA-MSR失效分析
五、FMEA-MSR风险分析
六、FMEA-MSR优化措施
1.通过AP分析,可以制定优化改进措施分别降低S/M/F
2.措施状态
3.有效性评估
七、FMEA-MSR标准化
第六章 返工返修FMEA
一、返工返修流程
二、返工返修流程FMEA
三、返工返修控制计划
第二篇 全套FMEA程序文件
第七章 PFMEA控制程序
一、PFMEA的目的
二、PFMEA的适用范围
三、PFMEA的参考文件
四、PFMEA的责任
五、PFMEA的程序重点
六、PFMEA的相关文件
七、PFMEA相关附件
1.PFMEA潜在失效模式及效应分析表
2.PFMEA结构树
3.PFMEA工艺流程图
4.PFMEA工作计划
第八章 DFMEA控制程序
一、DFMEA的目的
二、DFMEA的适用范围
三、DFMEA的参考文件
四、DFMEA的责任
五、DFMEA的程序重点
六、DFMEA的相关文件
七、DFMEA相关附件
1.DFMEA潜在失效模式及效应分析表
DFMEA边界图
3.DFMEA结构树
4.DFMEA工作计划
附录 考试测试题
答案
|
內容試閱:
|
导读
笔者在2017年8月出版了《五大质量工具详解及运用案例: APQP/FMEA/PPAP/MSA/SPC》,销量不错,读者的反馈很好。这本书包括FMEA的制作及相关案例,写得很详细,也很有操作性,基本上一看就知道如何使用FMEA。而2019年6月德国汽车工业协会VDA和美国汽车工业协会AIAG联合把第四版的FMEA标准进行修订,重新发行,并要求2019年6月的新产品都要用第五版的FMEA表格和思路。这个标准翻译成中文时,理解起来困难,看了国际标准,很多人还是云里雾里,到底要如何运用?要填写哪些表格?表格如何填写?为了解答这些问题,笔者决定把第五版FMEA新的做法写出来。
本书分为两篇,第一篇是是对FMEA标准的理解,用通俗易懂的语言告诉大家如何制作FMEA,有列出详细的步骤的案例。第一章FMEA基础知识,第二章PFMEA的制作步骤,第三章DFMEA的制作步骤,第四章软件DFMEA的制作步骤,第五章FMEA-MSR如何制作,第六章返工返修FMEA。第二篇是全套FMEA程序文件,包括DFMEA控制程序、PFMEA控制程序、FMEA工作计划、结构树、工艺流程图、参数图、FMEA表格等。
第五版FMEA基本上对整个FMEA进行了修改,比如失效影响的理解,以前只是说失效模式对客户造成的影响,现在新版的理解是,可以从三个方面来定义失效影响,从下工序、直接客户和最终使用者,这样定义更利于严重度的评分。新版RPN(风险顺序数)取消了,改为AP(措施优化级),现在采用AP措施优先级方式来确定要不要改善。原来PFMEA的发生度O评分,主要从不良率来评价,现在从预防措施的有效性、防错法来评价。失效模式有预防措施,分数低;没有预防措施的,分数高,有防错法的分数更低。
本书对DFMEA和产品图、产品规格书、包装规范的逻辑关系,PFMEA和工艺流程图、控制计划、作业指导书的逻辑关系进行了讲解,只有知道了他们的先后顺序及逻辑关系,才能灵活运用。
本书针对嵌入式软件进行了FMEA分析和讲解。
本书针对FMEA-MSR监视及系统响应的补充FMEA也是操作步骤及案例。FMEA-MSR的研究对象是软件系统、电子系统或机电系统,这些系统中至少包括一个传感器、一个控制单元和一个执行器,或它们的一个子集。FMEA-MSR可降低产品失效的严重度,比如刹车失灵,如果汽车刹车监视系统运作正常,我们可立即对刹车系统进行维修,这样刹车失灵的安全事故,严重度分数达到9分以上的,可降到6分或以下。
本书对旧版FMEA的程序文件、新旧版本表单的切换也做了详细说明,2019年6月后的新产品,建议按新版FMEA表格使用。
如果本书有错误,欢迎读者朋友指出,便于笔者进一步完善修改,更好地服务读者。
第一篇 FMEA详解第一章 FMEA的基础知识 一、什么是FMEA
FMEA(failure model effectiveness analysis),潜在失效模式与效应分析,效应分析也可翻译成后果分析,指潜在异常没有发生,可能会发生。FMEA一般是在正式设计或正式生产前做,是一种风险管理工具,目的是提高产品设计质量和工艺设计质量。
FMEA在20世纪60年代中期用于美国航天工业(NASA),是一项技术革新技术,70年代美国用于汽车行业的设计。1993年,在美国质量控制协会汽车部和汽车工业集团的主持下,克莱斯勒、福特和通用汽车公司对其各自有关FMEA的参考手册、程序、报告格式和技术术语进行标准化处理,形成统一的标准,这是第一版FMEA,现在我们用的是2019版,也就是第五版FMEA。第一版至第四版FMEA是美国汽车工业集团AIAG制作,第五版FMEA是AIAG和德国汽车工业协会VDA下属QMC质量管理中心制作。
FMEA的分类,按研究的时间来分,有设计DFMEA、过程PFMEA、监视和系统响应FMEA(FMEA-MSR),比如PCBA设计FMEA、PCBA过程FMEA。按研究的对象来分,有系统FMEA、子系统FMEA、部件FMEA,比如PCBA子系统PFMEA,研究印刷、贴片等工序失效,PCBA部件PFMEA,下面由PCB板、连接器、芯片等组成,可以有PCB工序PFMEA,研究锣板、钻孔、沉铜等工序的失效。如图1-1、图1-2所示。
图1-1系统FMEA分类图
图1-1-2 产品FMEA和过程FMEA分类图
FMEA-MSR是设计FMEA的一个补充,是研究汽车产品在使用过程中的监测诊断系统的失效,比如刹车异常亮黄灯,这就要刹车检测—传输信号—命令执行。FMEA-MSR的研究对象是软件系统、电子系统或机电系统,这些系统中包括至少一个传感器、一个控制单元和一个执行器,或它们的一个子集。分析有关在客户操作条件下的潜在失效,以及对系统和车辆的影响后果。该方法考虑的是系统或驾驶人员是否探测到失效。客户操作将被理解为终端用户操作,或服务操作和维护操作,包括车辆驾驶、维护保养、维修、软件更新升级等。在客户操作过程中发现失效,可以通过切换到降级操作,通知驾驶人员,和/或将诊断故障代码(DTC)写入控制单元达到服务目的,从而避免最初的失效模式。
二、FMEA的作用1.PFMEA的作用能够容易、低成本地对过程进行修改,从而减轻事后危机的修改。找到能够避免或减少这些潜在失效发生的措施。知识经验库,新员工的培训教材。生产控制计划和作业指导书制作的基础。减少生产过程的不良,预防不良找到措施。品质是设计出来的,要想提升品质,第一步是要提高工艺设计质量。2.DFMEA的作用能够容易、低成本地对产品进行修改,从而减轻事后危机的修改。找到能够避免或减少这些潜在失效发生的措施。知识经验库,为后续产品设计提供帮助,避免走弯路。制作测试和实验大纲的基础。避免量产后修改,增加公司的质量成本。更好地满足客户要求和法律法规要求。产品设计和创新是企业成功的根本,DFMEA可帮助企业找到更符合市场需求的设计方案。3.FMEA-MSR的作用
DFMEA的关注重点是产品的功能及失效分析,DFMEA中的“发生度(O)”和“探测度(D)”是与产品开发过程相关联的,是在开发过程中对功能实现情况的评估。而FMEA-MSR分析的是产品功能在被用户使用时,相关失效发生的“频度(F)”,已经发生失效时的可以被察觉发现的“监测度(M)”。因此,FMEA-MSR作为补充分析变得有用。FMEA-MSR评估当前的风险状态,并通过与可接受的剩余风险的条件进行比较,分析出额外监测的必要性。如果将产品的售后要求(异常自动报警、异常自动处理、维护、维修等)也纳入DFMEA的功能要求,那么FMEA-MSR分析可以是DFMEA的一部分。在做MSR设计时,各个功能点都是由各个客户操作来支持实现的。
4. FMEA作用图
从FMEA作用图可看出,产品设计问题和工艺设计问题,越早发现,解决品质问题的成本越低;越晚发现,解决问题的成本越高。所以,我们要通过FMEA这种工具尽早发现设计上的问题,把问题堵在量产前解决。如图1-3所示。
图1-3 FMEA作用图 三、谁来做FMEA
有三种人参加D/PFMEA的制作:一是协调员,负责整个FMEA的制作、评审、实施、有效评价、更新;二是核心团队,负责D/PFMEA的制作、评审、有效跟踪;三是扩展团队,负责FMEA的评审、实施。
DFMEA的制作人员如表1-1所示。
表1-1 设计DFMEA团队成员
小企业的核心成员主要是品质检验人员和工程部研发人员,包括结构工程、电子工程、软件工程。扩展团队就是生产主管、维修员、品质主管、采购代表、销售代表等。
PFMEA的团队成员如表1-2所示。
表1-2 PFMEA的团队成员
小企业的核心成员就是生产工程师、QA,扩展团队就是生产主管、维修员、品质主管、采购代表、销售代表、结构工程、电子工程、软件工程等。
建议PFMEA的制作,根据工艺流程图,各过程的负责人要参与PFMEA的评审修改,比如仓库负责原材料和成品仓储、搬运、运输的失效分析,IQC要负责原材料的失效分析,包装员要负责包装工序的失效分析,这样做出来的PFMEA充分有效,员工的认同度高,员工更愿意去落实预防措施,因为认识到了失效的原因和后果。
四、在什么时候做FMEA
一般FMEA的制作和更新有以下三种情况:
新设计、新技术或新过程。对现有设计或过程的修改。将现有的设计或过程用于新环境、新场所。
FMEA制作时间表如表1-3所示。
表1-3 FMEA制作时间表
FMEA类型
立项
产品设计
打样
工艺设计
试产
移交量产
DFMEA
启动DFMEA
DFMEA的预防和探测制作完成
第一次验证预防和探测措施有效性,修改DFMEA
再次验证预防和探测措施有效性,再次修改DFMEA
把预防和探测措施植入现有预防和探测中
PFMEA
启动PFMEA
PFMEA的预防和探测制作完成
验证预防和探测措施有效性,修改PFMEA
把预防和探测措施植入现有预防和探测中
五、DFMEA与PFMEA的不同
DFMEA是产品设计FMEA,包括系统设计、子系统设计、部件设计,是由客户和法律法规要求转化为产品功能性能、可靠性、结构、外观要求。比如一个水杯,客户和法律法规要求是能装多少毫升的水、材质要求、环保要求、外形要求,系统FMEA从这几个方面来做失效分析,找到设计改善要点。PFMEA研究的是工艺流程的失效,比如水杯,工艺流程是原材料—仓储—挤出—丝印—盖盖子—包装—仓储—出货,PFMEA是从工艺上找失效,能满足客户及法律法规要求,而且假设设计和上工序半成品没有问题。DFMEA的失效原因是从设计上寻找,PFMEA的失效原因是从人、机、料、法、环、测上去找。如表1-4所示。
表1-4 DFMEA和PFMEA的不同
不同点
DFMEA
PFMEA
失效模式
不能满足客户要求及法律法规要求、功能性能可靠性要求
不能满足工艺流程及功能要求
失效原因
设计上造成,比如结构设计不当、材料选用不当、软件有BUG、线路设计错误等
生产过程造成,比如员工技能不足、工艺参数设置错误、设备老化、刀具磨损等
失效影响
失效或不良对下一个系统造成的影响,比如部件FMEA对子系统FMEA造成的影响
失效或不良对下一工序或直接客户或间接客户造成的影响,比如水杯挤出不良对水杯组装、全检、包装造成的影响有返工返修等
预防
通过设计评审、防错法、设计规范、设计计算、仿真、经验教训、手工样检验评审、标杆分析
通过防错法、首检、4M1E的管理、控制图
探测
设计验证、确认,比如拉力测试、高低温实验等
巡检、自检、全检,通过目视、测量设备、实验等方式
六、系统、子系统、部件FMEA的不同
系统FMEA关注的是成品,比如一键启动装置;子系统FMEA关注的一个模组或半成品,比如PCBA或外壳;部件FMEA关注的是零件,比如电容、电阻、芯片、PCB板等。子系统FMEA的失效是从系统FMEA对它的要求来展开的,比如PCBA是子系统,分析这个失效要从系统一键启动这个成品对它的要求来展开分析,系统对它的要求不能满足,就是子系统的失效模式。如表1-5所示。
表1-5 系统、子系统、部件FMEA的不同
不同
设计
过程
系统
按照客户及法律法规要求做失效分析,比如产品环保、耐高温60度以上
成品组装各工序来做失效分析,比如装底座、装外壳失效分析
子系统
按照系统功能要求来做失效分析,比如高温60度以上PCBA也能正常通电
半成品各工序做失效分析,比如PCBA的印刷、贴装做失效分析
部件
按照子系统功能要求来做失效分析,比如零件全部要求环保材料
部件各工序做失效分析,比如PCB板的钻孔、沉铜、丝印做失效分析
七、FMEA的前提假设
做DFMEA的前提假设是生产过程和供应商没有问题,设计失效不能指望生产过程控制来解决,比如汽车的一键启动装置在60度以上也能正常工作,这个只能通过材料设计和电路设计来解决,不能通过供方管理、产品检验、生产过程管理来解决。
做PFMEA的前提假设是前工序的产品没有问题,设计没有问题。比如尺寸超差,只用通过设备、模具、工艺来解决,不能动不动改检验标准,改设计的工艺尺寸及公差。
|
|