新書推薦:
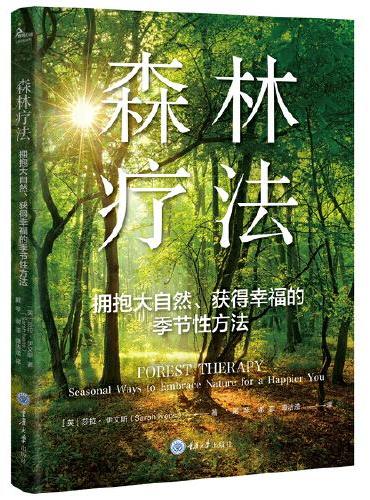
《
森林疗法:拥抱大自然、获得幸福的季节性方法
》
售價:NT$
340.0
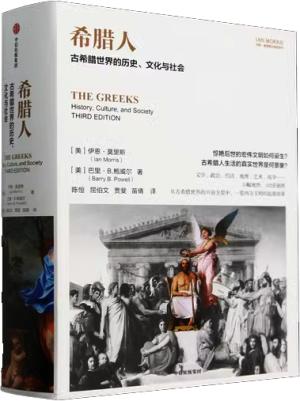
《
希腊人(伊恩·莫里斯文明史系列)
》
售價:NT$
845.0
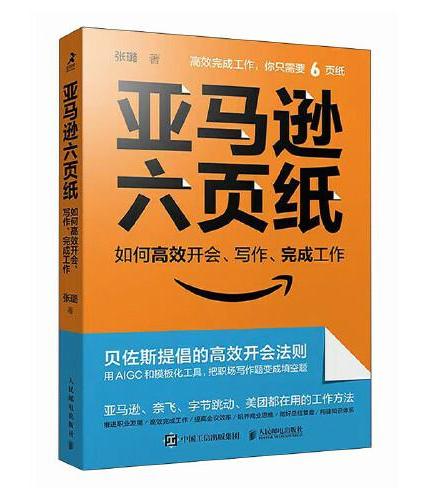
《
亚马逊六页纸 如何高效开会、写作、完成工作
》
售價:NT$
349.0
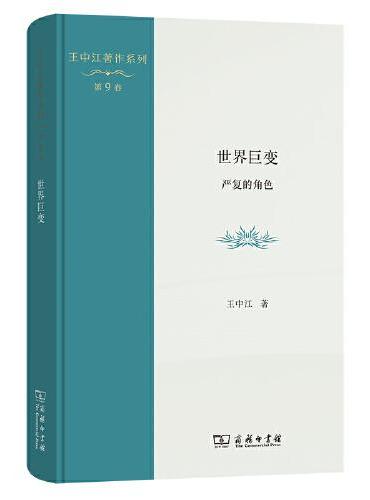
《
世界巨变:严复的角色(王中江著作系列)
》
售價:NT$
500.0
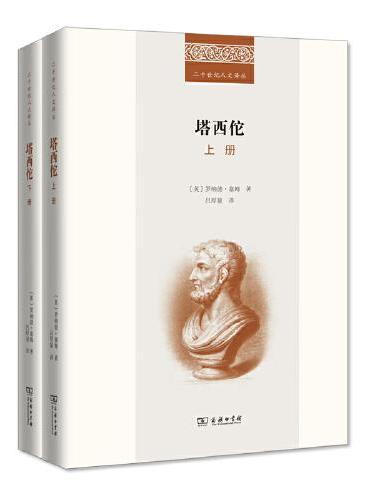
《
塔西佗(全二册)(二十世纪人文译丛)
》
售價:NT$
1800.0

《
(棱镜精装人文译丛)思想的假死
》
售價:NT$
290.0
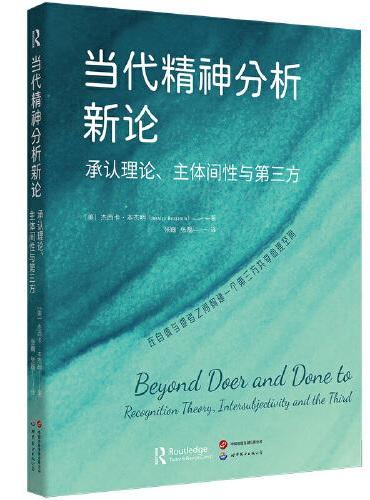
《
当代精神分析新论
》
售價:NT$
430.0
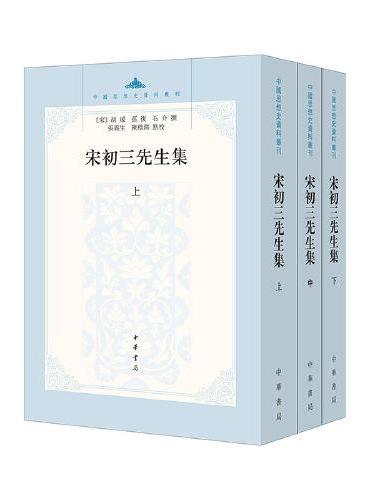
《
宋初三先生集(中国思想史资料丛刊)
》
售價:NT$
990.0
|
編輯推薦: |
所谓TPM(Total Productive Maintenance&Management),简单的说就是企业全员参与设备的维修管理。TPM起源 60年代起源于美国的PM(预防保安),经过日本人的扩展及创新,于81年形成了全公司的TPM(全面生产管理),并在日本取得巨大成功,随之在世界各地推广开来。目前已在众多国家和企业广泛应用,其效果被广为称赞。TPM作为一种自主维护活动,不仅能够降低损失,还能够预防生产现场中各种事故的发生,是一种重视现场的思考方式。企业若想实现零故障、零事故、零损失,在实施企业战略计划和落实企业规章制度的同时,必须动员企业中的全体成员,尤其是生产一线的工人们来实现这一目标。 本书通过TPM的活动分析,认为使企业生产发生事故和故障、产生损失的生产系统中潜在着16大损失。 这16大损失可以分为三大类: 一是“阻碍设备效率的8种损失”; 二是“阻碍人员效率化的5种损失”; 三是“阻碍基本单位(原料效率化)的3种损失”。 TPM活动通过将生产系统潜在的这16大损失降低为零,达到扩大企业效益和盈利的目的。而具体开展TPM活动时,“促进生产效率化的个别改善活动;构建以操作人
|
關於作者: |
JIPM-S:成立于2005年,是日本能率协会的法人之一。以制造业为对象,对工厂的设备改善、作业改善进行支援的咨询组织,向工厂派遣TPM等手法的指导人员。在相关培训和出版业务上也有涉足。
|
目錄:
|
前言 001
第1章 看漫画,识设备001
最懂设备的人是我们! 003
第2章 从TPM中学习提升现场力的秘诀
1.以构建舒适的工作环境为目标
2.目标是零灾害、零缺陷、零故障
3.体验自我成长的工作岗位
4.充分发挥团队力量
5.全员参加的体制改善从“干劲儿”、“能力”和“ 施展空间”开始
6.通过复合式团队为工作岗位注入活力
7.明确领导和成员各自的职责
8.自己的设备自己维护
9.做一个自律的操作人员
10.避免纸上空谈,应从现场入手(推荐三现主义)
11.清扫就是点检——理解设备结构的第一步
12.切断“差错”的发生源——维持设备的正常运转
13.从强制劣化到自然劣化
14.完善基础条件(清扫、注油、紧固)
15.检查设备的“健康情况”,以“应有状态”为目标
16.分步实施,推动人员和设备的体制改善
17.步步诊断式,即时体验成果
18.发现异常,复原异常——注意设备的异常
19.挂签、摘签——发现设备和工作中的异常!
20.对“看不见的异常”也要挂签
21.使用“可视化”图表,让人一目了然
22.为了减少“失误”
23.运用“目视管理”洞悉异常信号
24.运用“三件神器”激发活力
25.使TPM活动“可视化”的必不可少的TPM活动板
26.One Point Lesson表的真正作用
27.令人意外的会议运作的重要性
第3章 实现持续改善的秘诀
28.“改善之星”要通过现场、现物把握现状
29.改善之前先复原
30.时刻铭记“E·C·R·S”改善原则
31.即时可行的改善和确定主题后实行计划性推进的改善
32.用QC的问题解决法推动课题改善(把握现状~确认效果、制止)
33.熟练运用 QC七工具——各“工具”的作用
34.从故障中学习,以防再次发生
35.TPM“个别改善”的要点
36.找出企业利润大敌——“损失”
37.改善的最大着眼点是“现场的潜在损失”
38.让损失可视化,寻求改善方向
39.运用IE手法改善作业损失和浪费
40.挑战有助于缩短作业所需时间的“程序改善”
41.使用不花钱的智慧——“机关改善”的要点
反复追问“为什么”,追查真因
43.掌握“原理原则”,才不会得过且过!
44.坚持零化策略,探究一切要因
45.在工序间营造品质的“零缺陷机制”
46.根据4M检核法制作QM矩阵!
47.改善隐患就是预防重大事故
48.活用安全警示“黄签”,防灾于未然
49.以本质安全化确保工作岗位的安全
50.非常态化作业与灾害的关系
51.运用KYK、KYT、故障安全防护和愚巧装置
附录 TPM总复习
|
內容試閱:
|
1.以构建舒适的工作环境为目标 你所在的企业是否为员工提供了一个人性化的工作环境?下面就让我们一起通过TPM活动改善工作中的困扰,构建一个让员工安心放心和充满活力的工作环境! ■我们的工作岗位真的便于工作吗? 一天之中有三分之一以上的时间我们都是在工作场所度过的。那么它是一个人性化的工作环境吗?那里的机器设备是不是“故障频发”;“是否短暂停机的次数频繁、恢复正常运转所需的时间很长”;“经常出现不良产品,经常延时作业”,你有没有为这些问题感到困扰呢?另外,操作过程中你是不是经常碰到比如“不好干的活儿被搁置”、“始终跑来跑去,工作效率低下”、“重体力劳动多,身体疲惫”、“返工和重复操作频繁,无效操作多”等超负荷、浪费、不均衡的困扰呢?在工作环境方面,你是不是经常为“地面上沾满油污或粉尘,脚下一步一打滑”、“差点被机器夹住手,每次想起来就一身冷汗”之类不安全的工作环境感到忧心忡忡呢? ■通过TPM让工作更轻松 如果没有上面列举的问题,工作就好干多了,那样的环境应该是很人性化的了。企业一线员工要想解决生产现场的困扰,应从实践TPM(参考附录)开始。TPM作为一种改善生产现场、培养人才(引导员工自主成长)的有效机制已经被很多工厂引进并实践。 第一次接触TPM的人可能会担心TPM会不会造成额外的工作负担。没错!解决困扰大家已久的问题必须具备一定的力度。但是,如果对生产现场的问题置之不理,有谁会愿意在那样的工作环境中工作呢? 对从事生产的人来说,改善生产设备和客观环境也是工作的一部分。那么,为什么不通过推行TPM活动把从事生产的人从时间中解放出来,让他们工作起来更轻松,并逐步推进改善呢? 2.目标是零灾害、零缺陷、零故障 每天故障频发绝不是一个人性化的工作环境。那么就让我们一起从工作岗位抓起,把影响生产活动的问题——灾害、缺陷、故障降低为零,帮助员工减轻工作中的心理压力! ■什么是人性化的工作环境? 什么是影响每天生产活动的问题?是“灾害、缺陷、故障”。如果这些问题频发,就会导致生产无法按计划完成。一个让一线作业人员感到潜在受伤危险、缺陷、故障和短暂停机等精神压力的工作岗位很难被称之为一个人性化的工作环境。构建“人性化的工作环境”的目标,根本在于维持消除了生产活动中的问题的状态——“零灾害、零缺陷、零故障”。 ■零损失就是“减少活动 预防活动” 将损失降至为零,必须进行减少和预防损失的活动。所谓“减少损失的活动”,就是根据理论追溯已经发生的缺陷和故障的要因,并对这些要因进行复原和改善。但是,这一步只是事后对策,仅仅通过这些措施还不能将损失降至为零,这时更重要的是开展预防损失的活动。那么,为什么会发生“灾害、缺陷、故障”呢?问题出在作业人员对生产现场的异常的搁置。实践“零损失”的原则是:通过五观和“目视化管理”使异常提前“显现”(在问题发生之前发现并处理),防灾害于未然。在设备异常发生之前发现引起危险和顾虑的因素、缺陷和故障的潜在的发生源。并通过彻底使之消除的维护管理实现“零灾害、零缺陷、零故障”。 ■将“灾害、缺陷、故障”降低为零 将损失降至为零的设想是描述问题“应有的理想状态”并努力使之实现。也就是说,“追求极限”的挑战精神和“必须实现零目标”的信念最重要。 3.体验自我成长的工作岗位 体验自我成长必须付出相应的努力,首先是“干劲儿”;其次是“技能”和“施展空间”。具备了这些条件之后,让我们一起向构建人性化的工作环境发起挑战吧! ■第一步,尝试“成功体验”! “自主维护活动”(参见附录)是指由作业人员自己动手“改装设备”,在将损失降低至零的过程中提高自身技能,从而实现“人性化的工作环境”。 第一步是动力激发。对有“干劲儿”的作业人员来说,他们的目标是积极提高自身的能力(知识、技能、技术)。如果想让员工们工作中始终保持“干劲儿”,则必须有活动的成果——“成功体验”,因为体验目标实现时的喜悦并积累成功非常重要。 ■体验成长 当TPM活动逐渐步入正轨时,××企业新入职的员工小A第一次开始倒班工作。此后不久,小A在生产现场巡逻的过程中无意中发现地板上沾了一滴油污,很快他把这件事汇报给上级。由于小A的早期发现,使一场因阀门漏油可能引发的重大事故得以避免,在相关人员采取应急措施维修后,生产恢复正常。企业一线员工通过对车间地板进行彻底清扫和干燥处理,这和实现自主维护的出发点——“异常现象早发现”的成果是分不开的。 如上所述,通过自主改善所在的生产现场和工作环境,发现工作中存在的异常现象并获得成功体验,进而感受到维护管理和防患于未然的重要性。这样的生产一线才能被称之为“员工体验自我成长的工作环境”。
|
|