新書推薦:
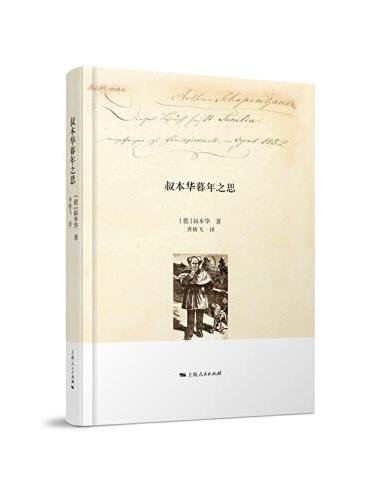
《
叔本华暮年之思
》
售價:NT$
325.0
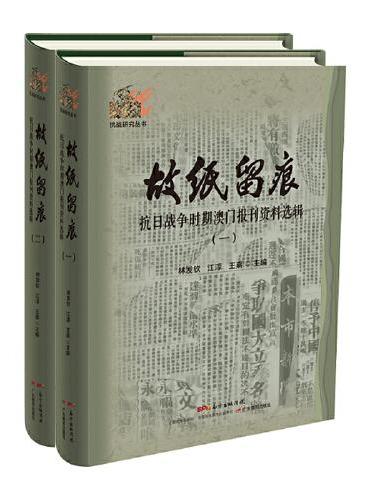
《
故纸留痕:抗日战争时期澳门报刊资料选辑
》
售價:NT$
1613.0

《
玩转Photoshop(零基础快速上手,全彩赠视频)
》
售價:NT$
269.0
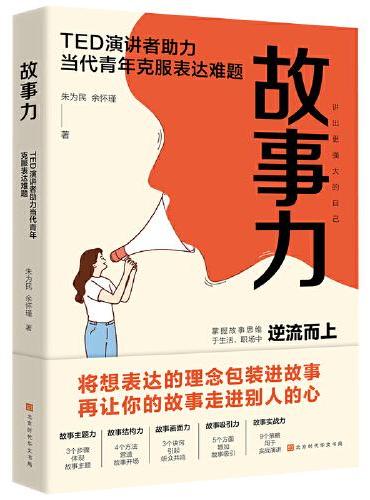
《
故事力:TED演讲者助力,当代青年克服表达难题(两位TED专业讲者教你掌握故事五大力)
》
售價:NT$
381.0
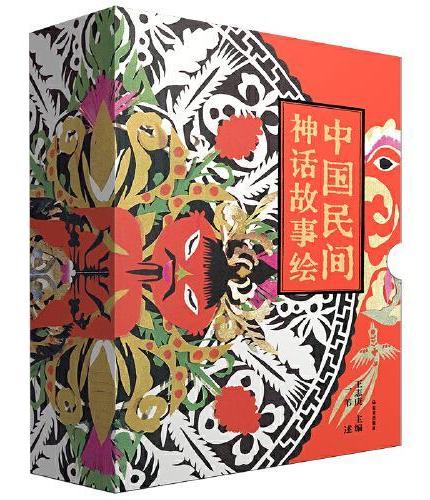
《
中国民间神话故事绘(套装共15册)
》
售價:NT$
2128.0
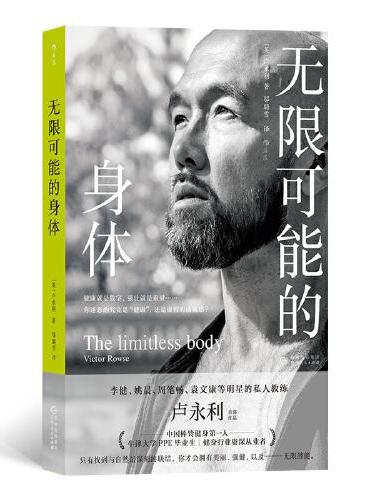
《
无限可能的身体
》
售價:NT$
336.0
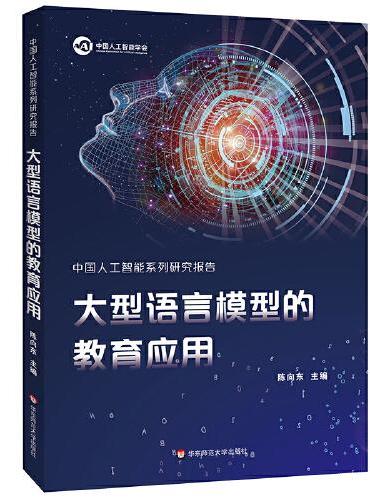
《
中国人工智能系列研究报告:大型语言模型的教育应用
》
售價:NT$
325.0
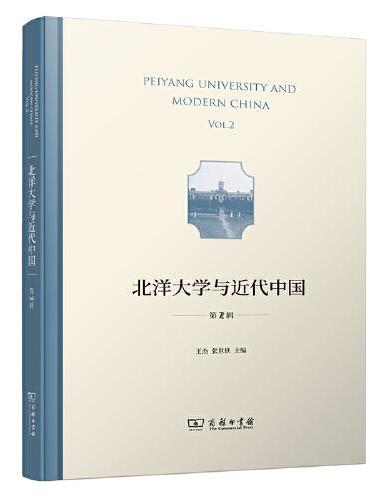
《
北洋大学与近代中国(第2辑)
》
售價:NT$
717.0
|
內容簡介: |
《提升钢丝绳的摩擦可靠性》内容分为两篇,共11章。**篇基于提升钢丝绳的摩擦传动可靠性,主要建立摩擦式提升系统钢丝绳动张力、钢丝绳与摩擦衬垫动态接触及蠕动仿真模型,研究钢丝绳与摩擦衬垫之间的动态黏弹性摩擦机理,揭示摩擦式提升系统动态摩擦传动机理,基于摩擦提升系统振动模型建立钢丝绳动力学与摩擦稳定性的耦合关系,优化提升机运行参数来提高摩擦传动可靠性和平稳性。第二篇围绕提升钢丝绳的摩擦疲劳可靠性问题,提出提升钢丝绳的微动损伤理论,研究了钢丝绳内部钢丝微动磨损、微动疲劳、微动腐蚀、拉扭复合等工况对钢丝绳的损伤及可靠性的影响,建立钢丝绳微动磨损理论模型、磨损深度演化方程和微动摩擦疲劳模型,提出基于钢丝磨损的钢丝绳安全系数预测模型。
|
目錄:
|
目录
前言
变量注释表
总论 1
0.1 钢丝绳作为摩擦式提升机的重要传动部件 1
0.2 钢丝绳作为提升机的关键承载部件 4
参考文献 7
**篇 提升钢丝绳的摩擦传动可靠性
第1章 提升钢丝绳动张力的理论建模 13
1.1 数学模型 13
1.2 Simulink仿真模型 15
1.2.1 仿真模型数值分析 15
1.2.2 仿真模型 16
1.2.3 仿真模型设置 17
1.3 计算实例 17
1.3.1 钢丝绳动张力分析 17
1.3.2 **提升速度对动张力的影响 18
1.3.3 提升加速度对动张力的影响 20
1.3.4 提升终端质量对动张力的影响 22
1.4 钢丝绳动张力的验证 24
1.4.1 实验平台原理 24
1.4.2 主要参数 25
1.4.3 实验验证 26
1.5 本章小结 27
参考文献 27
第2章 钢丝绳与摩擦衬垫的黏弹性摩擦机理 28
2.1 钢丝绳与摩擦衬垫静态摩擦测试 28
2.2 “弧面法”摩擦试验机的研制 29
2.3 摩擦衬垫摩擦系数的确定方法 31
2.4 基于弧面法摩擦衬垫的摩擦性能研究 33
2.4.1 干摩擦条件下 34
2.4.2 淋水条件下 34
2.4.3 涂增摩油脂条件下 35
2.4.4 动态载荷下 36
2.4.5 变加载速度下 37
2.4.6 弧面法与平面法的对比 38
2.5 摩擦衬垫的滑动摩擦机理研究 39
2.5.1 衬垫特性与摩擦性能关系 39
2.5.2 衬垫基本性能对摩擦性能的影响 39
2.5.3 衬垫黏弹特性对摩擦性能的影响 40
2.6 摩擦衬垫与钢丝绳的黏弹性接触机理 42
2.6.1 动态加载过程中实时动态原位观测 42
2.6.2 摩擦过程中接触界面的接触状态 43
2.6.3 摩擦过程中接触界面的原位形貌观测 44
2.6.4 单摩擦周期内衬垫表面瞬时摩擦机理研究 46
2.6.5 整个实验过程中衬垫表面的摩擦机理 47
2.7 摩擦衬垫接触界面的磨损分析 47
2.7.1 摩擦衬垫接触表面的磨损形貌 47
2.7.2 K25衬垫接触界面的磨损形貌 48
2.7.3 K25衬垫磨屑的红外光谱 49
2.8 本章小结 50
参考文献 50
第3章 提升钢丝绳的摩擦传动可靠性 52
3.1 钢丝绳动态摩擦传动的提出 52
3.2 摩擦弧域安全准则 56
3.2.1 动态摩擦弧理论 56
3.2.2 动态摩擦弧与安全储备 59
3.2.3 动态摩擦传动弧段划分 60
3.3 钢丝绳与摩擦衬垫的动态接触 65
3.3.1 数学模型 65
3.3.2 仿真模型 66
3.3.3 实例分析 67
3.4 钢丝绳与摩擦衬垫的动态蠕动 68
3.4.1 数学模型 68
3.4.2 仿真模型 70
3.4.3 实例分析 70
3.4.4 实验验证 75
3.5 本章小结 76
参考文献 76
第4章 提升钢丝绳的摩擦传动平稳性 78
4.1 钢丝绳横-纵振动 78
4.1.1 AdamsCable仿真模型 78
4.1.2 钢丝绳的振动特性 79
4.2 特殊工况下的钢丝绳平稳性 85
4.2.1 制动工况下钢丝绳的动力学分析 88
4.2.2 卡顿工况下钢丝绳的动力学分析 91
4.2.3 激励工况下钢丝绳的动力学分析 93
4.3 正常提升工况下钢丝绳的传动平稳性 100
4.3.1 钢丝绳卷绕动力学 100
4.3.2 局部动态摩擦力 103
4.3.3 钢丝绳振动与摩擦传动关联性 105
4.4 本章小结 109
参考文献 109
第5章 摩擦传动平稳可靠性优化及应用 112
5.1 摩擦传动参数优化 112
5.1.1 钢丝绳张力控制 112
5.1.2 钢丝绳振动控制 118
5.2 实际摩擦式提升系统模型建立及应用 124
5.2.1 提升机设备 124
5.2.2 提升机振动实测数据 126
5.2.3 实际摩擦式提升系统仿真模型 131
5.2.4 仿真结果验证 132
5.2.5 摩擦传动可靠性参数评价 134
5.3 本章小结 143
参考文献 144
第二篇 提升钢丝绳的摩擦疲劳可靠性
第6章 提升钢丝绳微动损伤和扭转参数确定 149
6.1 提升钢丝绳的微动损伤参数 149
6.1.1 钢丝拉力 150
6.1.2 钢丝间相对位移 150
6.1.3 钢丝间接触载荷 151
6.2 建模与仿真 151
6.2.1 **提升速度对微动疲劳参数的影响 151
6.2.2 提升加减速度对微动疲劳参数的影响 153
6.2.3 终端质量对微动疲劳参数的影响 154
6.3 扭转参数计算 156
6.3.1 钢丝绳动张力 156
6.3.2 钢丝绳扭转角 157
6.3.3 钢丝绳内部绳股扭转角 158
6.3.4 绳股内部钢丝扭转角 159
6.4 本章小结 160
参考文献 160
第7章 钢丝的微动磨损理论 161
7.1 微动磨损试验机的研制 161
7.1.1 钢丝参数 161
7.1.2 试验参数 162
7.1.3 摩擦系数计算方法 162
7.1.4 磨损量测量 162
7.2 钢丝的切向微动磨损研究 163
7.2.1 接触角度90°时钢丝摩擦副的切向微动磨损行为 163
7.2.2 接触角度18°时钢丝摩擦副的切向微动磨损行为 174
7.2.3 钢丝切向微动磨损特性的综合分析 183
7.3 腐蚀环境下钢丝的微动磨损研究 188
7.3.1 酸性腐蚀介质下钢丝的微动磨损特性 188
7.3.2 中性腐蚀介质下钢丝的微动磨损特性 199
7.3.3 碱性腐蚀介质下钢丝的微动磨损特性 209
7.3.4 四种环境下钢丝微动磨损行为的比较 218
7.4 本章小结 223
参考文献 223
第8章 钢丝的微动疲劳理论 224
8.1 拉-拉拉-扭微动疲劳试验机的研制 224
8.1.1 钢丝拉-拉微动疲劳试验装置 224
8.1.2 钢丝拉-扭多轴微动疲劳试验装置 226
8.2 90°接触角度下钢丝微动疲劳行为 229
8.2.1 不同接触载荷下钢丝微动疲劳行为 229
8.2.2 不同应变比下钢丝微动疲劳行为 234
8.3 18°接触角度下钢丝微动疲劳行为 246
8.3.1 不同接触载荷下钢丝微动疲劳行为 246
8.3.2 不同应变比下钢丝微动疲劳行为 252
8.3.3 不同**应变下钢丝微动疲劳行为 261
8.4 不同接触角度下钢丝微动疲劳行为 264
8.4.1 微动运行特征曲线和工况图 264
8.4.2 摩擦系数 265
8.4.3 磨损分析 266
8.4.4 微动磨痕形貌 268
8.4.5 微动疲劳寿命 270
8.5 腐蚀环境下钢丝的微动疲劳研究 270
8.5.1 碱性腐蚀介质下钢丝的微动疲劳特性 270
8.5.2 中性腐蚀介质下钢丝的微动疲劳特性 278
8.5.3 酸性腐蚀介质下钢丝的微动疲劳特性 287
8.5.4 不同腐蚀介质下钢丝的微动疲劳特性对比分析 296
8.6 钢丝的拉-扭复合微动疲劳研究 303
8.6.1 90°交叉角下钢丝的拉-扭复合微动疲劳行为 303
8.6.2 交叉角为26.2°时钢丝拉-扭多轴微动疲劳实验研究 320
8.6.3 交叉角为26.2°和90°时钢丝拉-扭多轴微动疲劳行为对比研究 329
8.7 本章小结 332
参考文献 332
第9章 矿用钢丝的应力腐蚀与腐蚀疲劳 334
9.1 慢应变速率拉伸下钢丝的应力腐蚀行为 334
9.1.1 实验方法 334
9.1.2 拉伸曲线分析 335
9.1.3 断面收缩率分析 336
9.1.4 断口形貌分析 337
9.1.5 快慢极化曲线测量 340
9.2 恒应力拉伸下钢丝的应力腐蚀行为 342
9.2.1 实验方法 342
9.2.2 开路电位分析 342
9.2.3 EIS分析 343
9.3 不同腐蚀环境下钢丝的腐蚀疲劳行为 346
9.3.1 实验方法 346
9.3.2 不同腐蚀环境对钢丝CF行为的影响 346
9.3.3 不同外加电位对钢丝CF行为的影响 349
9.4 本章小结 353
参考文献 354
第10章 钢丝绳的疲劳损伤机理 355
10.1 钢丝绳疲劳试验机的研制 355
10.2 绕钢质滑轮钢丝绳的弯曲疲劳损伤行为 357
10.2.1 钢丝绳外部损伤 357
10.2.2 钢丝绳疲劳损伤量值演化 358
10.2.3 钢丝绳损伤机理 360
10.2.4 钢丝绳疲劳断口形貌 361
10.3 绕尼龙滑轮工作钢丝绳的弯曲疲劳损伤行为 363
10.3.1 钢丝绳外部损伤 363
10.3.2 钢丝绳疲劳损伤量值演化 365
10.3.3 钢丝绳的损伤机理分析 366
10.3.4 钢丝绳疲劳断口形貌 367
10.4 表面断丝对钢丝绳的弯曲疲劳性能影响 369
10.4.1 表面断丝钢丝绳的断丝分布规律 369
10.4.2 表面断丝钢丝绳的损伤量值 371
10.4.3 表面断丝捻距内钢丝绳的宏观形貌分析 372
10.4.4 表面断丝捻距内钢丝绳的SEM形貌分析 373
10.4.5 钢丝绳内部的微动磨痕形貌分析 375
10.5 表面磨损对钢丝绳的弯曲疲劳性能影响 376
10.5.1 表面磨损钢丝绳断丝分布规律 376
10.5.2 表面磨损钢丝绳的损伤量值 377
10.5.3 表面磨损捻距内钢丝绳的宏观形貌分析 378
10.5.4 表面磨损捻距内钢丝绳的SEM形貌分析 379
10.5.5 钢丝绳内部的微动磨痕形貌分析 382
10.6 表面腐蚀对钢丝绳的弯曲疲劳性能影响 383
10.6.1 表面腐蚀钢丝绳的损伤行为和断裂机理分析 383
10.6.2 表面腐蚀捻距内钢丝绳的SEM形貌分析 387
10.7 本章小结 389
参考文献 390
第11章 提升钢丝绳的摩擦疲劳可靠性预测 391
11.1 钢丝磨损预测模型 391
11.2 钢丝绳安全系数的预测模型 394
11.2.1 提升钢丝绳微动磨损参数计算 39
|
|