新書推薦:
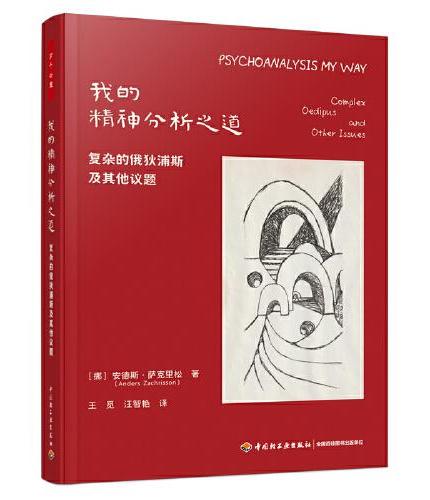
《
万千心理·我的精神分析之道:复杂的俄狄浦斯及其他议题
》
售價:NT$
475.0
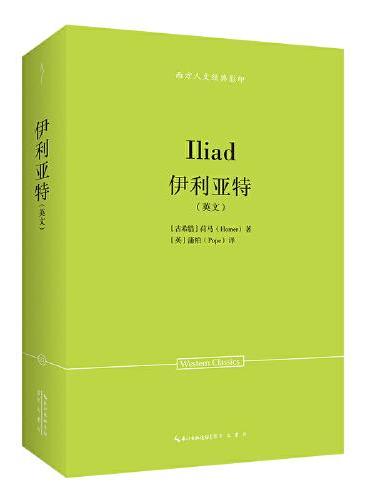
《
荷马:伊利亚特(英文)-西方人文经典影印21
》
售價:NT$
490.0
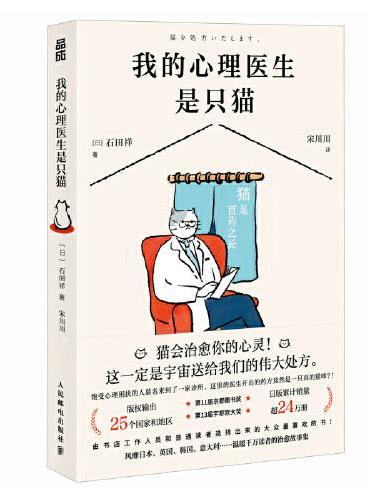
《
我的心理医生是只猫
》
售價:NT$
225.0
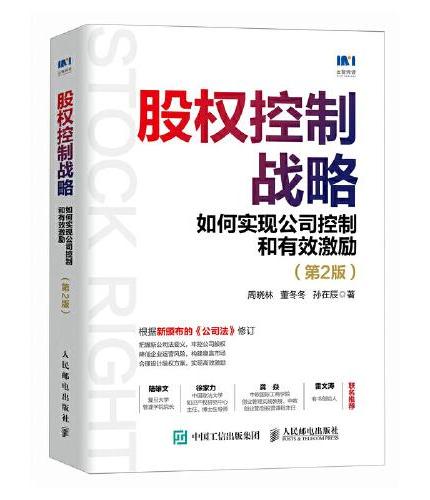
《
股权控制战略:如何实现公司控制和有效激励(第2版)
》
售價:NT$
449.0
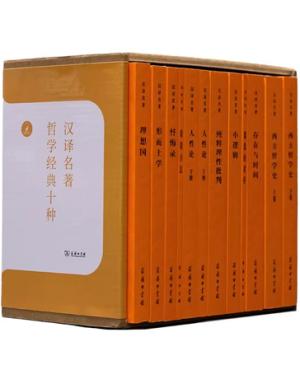
《
汉译名著·哲学经典十种
》
售價:NT$
3460.0
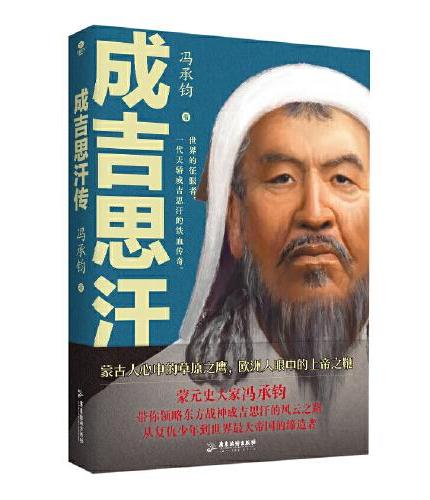
《
成吉思汗传:看历代帝王将相谋略 修炼安身成事之根本
》
售價:NT$
280.0
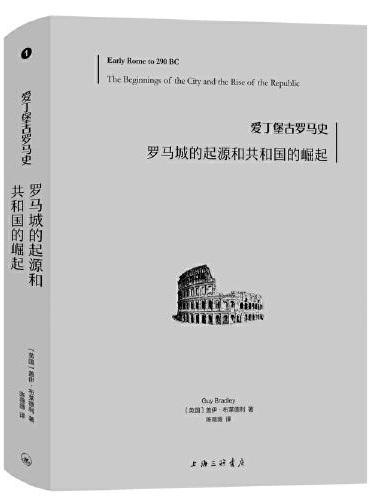
《
爱丁堡古罗马史-罗马城的起源和共和国的崛起
》
售價:NT$
349.0
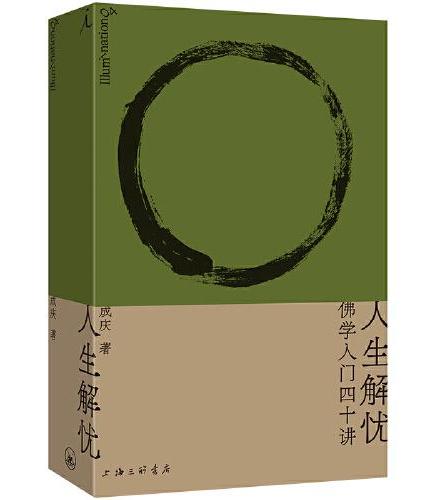
《
人生解忧:佛学入门四十讲
》
售價:NT$
490.0
|
編輯推薦: |
《机床主轴高精度动平衡技术》适合旋转机械、转子动力学、不平衡振动测试与诊断等相关领域的高校教师、研究生阅读,也可供从事旋转机械动平衡设计、开发及应用的工程技术人员参考。
|
內容簡介: |
《机床主轴高精度动平衡技术》分别从主轴系统动力学建模和振动信号处理两方面论述机床主轴动平衡问题,系统阐述机床主轴不平衡状态下动力学行为的分析理论,以及机床主轴不平衡状态在线监测、辨识和校正方法。主要内容包括机床主轴动平衡现状及发展趋势、主轴动平衡基础理论,以及主轴不平衡行为的力学分析及参数识别、不平衡振动抑制策略、动平衡中各向异性问题研究及平衡目标优化等,并介绍作者最新开展的机床主轴动平衡在线调整技术、不平衡振动信号分析与特征提取技术、主轴动平衡综合状态测控系统等研究内容。
|
目錄:
|
前言
第1章绪论
1.1机床主轴在装备制造业中的地位
1.2机床主轴高精度平衡面临的挑战
1.3机床主轴动平衡现状及发展趋势
1.3.1动平衡识别方法
1.3.2在线自动平衡技术
1.4本书目的
第2章机床主轴动平衡基础
2.1机床电主轴介绍
2.1.1电主轴结构及技术特点
2.1.2电主轴的技术优势
2.2机床主轴不平衡特征及平衡标准
2.2.1主轴不平衡机理特征
2.2.2主轴动平衡品质及评价标准
2.3机床主轴动平衡基本实现方法
2.3.1影响系数法
2.3.2其他平衡方法
2.4机床主轴动平衡精度影响因素分析
2.4.1系统非不平衡故障的影响
2.4.2主轴系统特性与平衡理论假设之间的差异
第3章主轴不平衡行为的力学分析及参数识别
3.1主轴轴承系统动力学建模
3.1.1轴承刚度计算
3.1.2复合预紧力计算
3.2主轴系统动力学模型及不平衡响应
3.2.1主轴单元分析
3.2.2系统运动方程
3.2.3临界转速与不平衡响应计算
3.3基于反问题数学模型的不平衡识别
3.3.1连续不平衡处理
3.3.2反问题数学模型
3.3.3仿真与实例分析
3.4不平衡求解中的病态问题研究
3.4.1不平衡平面组相关性定义
3.4.2基于基平面的不平衡力等效原则
3.4.3仿真及实验验证
3.5基于优化算法的不平衡识别策略
3.5.1优化问题构造
3.5.2粒子群算法
第4章基于模态分析的主轴不平衡振动抑制策略
4.1模态不平衡力等效原则
4.2基于低阶模态分析的振动抑制策略
4.2.1基于低阶模态力平衡的无试重方法
4.2.2主轴实验台仿真
4.3基于低阶模态分析的简化振动抑制策略
4.3.1基于模态力的反问题算法重构
4.3.2仿真与实验验证
4.4基于多阶模态分析的振动抑制策略
4.4.1基于多阶模态分析的无试重动平衡方法
4.4.2主轴实验台仿真
4.5不平衡振动抑制策略比较分析
4.5.1不同动平衡方法优缺点分析
4.5.2仿真与实验验证
第5章动平衡中各向异性问题研究及平衡目标优化
5.1各向异性转子不平衡响应及其对初相矢的影响
5.1.1各向异性转子不平衡响应及其对初相矢的影响
5.1.2仿真计算及分析
5.2转子进动特性分析及等效初相矢构建
5.2.1椭圆轨迹下转子进动特性分析
5.2.2等效初相矢的构建原理
5.3基于等效初相矢的改进全息动平衡方法
5.4动平衡实例验证
5.4.1等效初相矢有效性验证
5.4.2现场动平衡验证
第6章机床主轴动平衡在线调整技术
6.1动平衡调整技术概述
6.1.1离线动平衡
6.1.2现场动平衡
6.1.3在线动平衡
6.2注液式在线自动平衡控制技术
6.2.1工作原理及平衡终端设计
6.2.2平衡装置测控系统设计
6.2.3平衡装置性能分析
6.2.4平衡系统喷液精度分析
6.2.5控制策略及系统验证
6.3压电式在线自动平衡控制技术
6.3.1压电式在线动平衡装置的整体实现方案
6.3.2压电式调整机构的结构设计与工作机理
6.3.3非接触感应式电能传输系统的设计
6.4其他在线自动平衡控制技术
6.4.1电机驱动式在线动平衡技术
6.4.2电磁式在线动平衡技术
6.5便携式现场动平衡测试仪
第7章主轴振动信号分析与特征提取技术
7.1全息谱故障诊断技术
7.1.1二维全息谱
7.1.2三维全息谱
7.2误差分离技术在全息故障诊断中的应用
7.2.1截面轮廓误差对全息谱的影响分析
7.2.2三点法误差分离技术及其优化
7.2.3误差分离技术在全息谱中应用
7.3基于谐波小波的振动信号提纯技术
7.3.1谐波小波滤波原理
7.3.2主轴回转误差的提纯
7.3.3主轴失衡振动提取
7.4基于转频振动消减原理的失衡振动提取技术
7.4.1转频振动消减原理
7.4.2实验验证
7.5基于自适应滤波方法的快变失衡振动提取技术
7.5.1基于NLMS算法的失衡振动提取技术
7.5.2基于RLS算法的失衡振动提取技术
第8章机床主轴动平衡综合状态测控系统
8.1主轴状态综合监测技术概述
8.1.1振动测试传感器
8.1.2国内外主轴状态监测技术
8.2测控系统总体方案
8.3测控系统硬件设计
8.3.1硬件总体架构
8.3.2硬件参数设计
8.3.3采样控制电路
8.4测控系统软件设计
8.4.1软件总体架构
8.4.2软件设计关键技术
8.5测控系统实现
8.6实例验证
8.6.1150SD40Q7型高速主轴测试
8.6.2HF1704A20型主轴测试
参考文献
|
內容試閱:
|
第1章绪论
1.1机床主轴在装备制造业中的地位
高速切削加工(highspeedmachining)的概念由德国切削物理学家Salmon在1931年提出。他在金属材料切削实验中发现,尽管切削温度会随着切削速度的增加而急剧上升,但切削速度超过某一临界值时,切削温度就不再表现出单调上升的趋势,反而随着切削速度的升高而减小,从而越过切削过程产生的高温死区(deadvalley),使**能在超高速区域进行高速切削。
机床主轴切削速度的提升意味着加工效率的提高,并且切削速度越高,切削激励力越远离机床的低阶固有频率,加工质量将得到显著提高,由此可达到高效率、高精度的完美结合。此外,高速机床可切削硬度在HRC45~65的淬硬钢,避免了淬火变形,有利于切削难加工材料。因此,高速切削技术逐步成为切削加工的主流,其在航空航天、能源、高速机车等行业已得到广泛应用。目前,航空航天业加工中钛合金的切削速度可达60~240mmin,镍基合金的切削速度可达50~200mmin,而现有飞机整体结构件和航空发动机主要构件则全部采用高效切削加工技术[1,2]。
未来的装备制造行业正朝着高速、高精度方向发展,迫切需要精准的数字装备予以支撑,而机床主轴系统是现代高档数控机床的关键部件,数控机床的加工效果很大程度上取决于主轴性能[3,4]。机床主轴作为超高速加工的核心功能部件,其性能直接制约着超高速加工技术的发展。不同于传统的加工主轴,电主轴将变频电机的空心转子与机床主轴过盈套装,带冷却套的定子则装配在主轴单元的壳体内,从而将机床主轴与电机的功能从结构上融为一体,把机床主传动链的长度缩短为零,实现了变频电机和机床主轴之间的“零传动”[5],避免了传动链导入的振动和误差,提高了回转精度。此外,电主轴启停快,能实现较高角加速度,采用矢量控制调速技术,调速范围宽,输出功率大。图1-1为典型电主轴结构示意图。
中国是世界第一的机床消费大国,但由于我国高速加工理论研究基础薄弱,缺乏核心技术,在重大专项中规划的机床最高转速、加工精度等技术指标与国外还有较大的差距,大型高速精密数控机床多数需要进口。因此,《国家中长期科学和技术发展规划纲要(2006—2020年)》已将高性能机床及基础装备列为16项重大专项之一。作为机床关键组件之一,国产电主轴的各项指标与国外产品相比都有较大差异,而且国产电主轴在使用中还存在许多亟待解决的问题,远远不能满足日益发展的国内市场的需要;再加上长期以来对研究的投入严重不足和高档产品对进口的依赖,使得国内拥有自主知识产权的电主轴更是凤毛麟角。目前我国大功率高速主轴单元主要依赖进口,高速电主轴几乎占机床价格的13。因此,研究和发展高速电主轴技术,对国产高性能机床和国内制造业的发展具有重要意义。
图1-1典型电主轴结构示意图
1.2机床主轴高精度平衡面临的挑战
机床主轴作为典型的旋转机械,不平衡是常见的故障。不平衡又称为偏心,即主轴的旋转中心与质量中心不重合。不平衡的存在会使主轴旋转过程中产生方向不断变化的离心力,进而激发机械振动,影响主轴运行状态和工件的加工质量,严重时引起主轴损坏甚至引发事故。对于主轴而言,不平衡的存在是必然的,在主轴的设计、制造和使用过程中,都会引起质量分布的不均匀。主轴设计上存在的不对称结构,主轴材质密度的不均匀分布,主轴加工装配过程中存在的误差,主轴使用过程中出现的磨损、脱落、粘灰、**更换等因素都会导致主轴不平衡。
目前机械转子的工作转速通常在10000rmin以下,径向振动量通常在10μm数量级,而高速主轴的旋转速度在30000rmin以上,径向振动量要求控制在1μm数量级。而高速下主轴的微小不平衡将可能导致回转精度的严重丧失,乃至轴承支承的损坏。因此对高速主轴不平衡控制的要求比通常转子更加严格,另外,主轴系统还要受到换刀、切削力激励以及主轴**系统受热变形和高速旋转离心力等复杂工况干扰,高速机床主轴系统的稳定性控制受到空前挑战。为减小主轴的不平衡,在设计之初应尽量避免不对称结构,在加工装配过程中尽量减小误差。即便如此,主轴不平衡也不可能完全消除。在工业上一般采用动平衡的方法来减小或消除主轴的不平衡量,以达到减小振动、提高主轴运行精度和工件加工质量的目的。然而,在机床主轴技术的飞速发展的同时,也给现有的动平衡方法带来了新的挑战[6]。
1)支承形式的复杂化
传统主轴以滚动轴承支承,滚动轴承在高速运行中存在摩擦发热严重、回转误差较大、润滑冷却困难等问题。流体动静压滑动轴承、气浮轴承、磁悬浮轴承等由于其独特的技术优势而越来越多地应用于高速主轴,但支承形式的多样化也会给失衡故障的确诊和失衡响应的提取带来困难。此外,主轴系统通常表现出各向异性,一方面受轴承技术和工况影响,轴承的刚度和阻尼为各向异性;另一方面受加工工艺限制,主轴转子本身在圆周方向上的主惯矩不等,导致结构上的各向异性等。显然,对于这类支承刚度具有一定各向异性的转子而言,转子测量截面的单方向振动并不能精确地描述转子振动状态[7]。因此,主轴支承方式的多样化,尤其是支承各向异性的存在,对主轴动平衡提出了新的需求,有必要研究有效的失衡故障定性诊断方法和精确的失衡响应提取技术。与此同时,探寻新的适应各向异性转子的失衡表征量,提出满足各向异性转子平衡需求的动平衡方法也是焦点所在。
2)主轴转子的柔性化
传统的加工中心主轴由于要承受大的切削力,往往采用高刚性设计以保证加工精度。由于超高速加工有常规加工所不具有的优势,高速切削技术已成为装备制造业发展的主流。然而,主轴工作转速的升高将会导致主轴轴径减小,这主要由两方面因素导致:一方面,主轴工作转速升高带来的是主轴离心力的指数增长和摩擦发热的迅速增加,并且主轴轴径越大,轴承及最外层材料受到的离心力就越大,同时主轴最外层的线速度也越高,摩擦发热也越严重,因此,在高速主轴中要想取得更高的转速,必须减小轴径以减小主轴所受到的离心力和主轴的摩擦发热;另一方面,主轴的dmn值(主轴轴承中径dm与转速n的乘积)越高意味着同样轴径的主轴所能达到的转速也越高,dmn成为衡量主轴技术水平重要标准。但是,dmn值越大,离心力和摩擦发热越严重,而材料所能承受的离心力和温度总是有限的,即dmn不可能无限增加,因此,在dmn相同的情况下,要提高主轴转速,只有减小轴径。显然,轴径的减小意味着转子刚度下降,这必然导致主轴转子在高转速下向柔性化发展,而Salmon认为,当切削速度达到并超过某临界值时,切削温度和切削力不但不会增加反而会减小,从而可以越过切削过程产生的高温死区,使**在超高速区域进行高速切削。这表明低刚度的主轴应用于高速切削加工的是可能的。虽然由于诸多技术难题的存在,柔性主轴的实用化还有很长一段路要走,但国内外学者已经就柔性主轴展开了大量的研究工作,高速主轴的柔性化已经成为一种趋势。在超高速下主轴的平衡要求更加苛刻,原有的基于集中质量式假设的力学模型难以满足高精度的平衡识别需求,因此,开展针对柔性主轴的分布式不平衡量识别研究也是研究重点。
3)动平衡控制的在线自动化
现代化的高速数控加工中心具有主轴转速高、运行精度高和加工效率高的特点。机床主轴转速和精度的提高,是以高精度动平衡为前提的,只有将主轴的残余不平衡量控制在微小范围内,才能控制主轴在高速运行过程中由离心力引起的失衡振动,保证零件的加工精度。然而,在实际加工过程中,尽管主轴出厂时会进行高速动平衡,但主轴换刀时**微小的不对中、磨损或粘刀都会破坏原有的动平衡。另外主轴高速旋转时还会带来离心膨胀作用,如主轴组件中拉刀机构的离心变形等,也会破坏主轴的动平衡。显然,若每次都采用传统离线停机动平衡的方式来消除微小失衡量,则意味着自动化环节的中断,破坏了高效加工的原则,在现代化加工中是无法接受的。因此,有必要研制高速主轴在线自动平衡系统,对主轴在高速运转情况下的平衡状态进行实时监测,并通过在线动平衡控制来减小由此产生的振动,以提高主轴平衡效率,保证主轴的运行精度,保障机床的长期稳定和高效运行。
综上所述,开展机床主轴高精度动平衡技术研究,能充分发挥高速电主轴的效能,进而提高我国机床工业和机械制造业的整体水平。
1.3机床主轴动平衡现状及发展趋势
1.3.1动平衡识别方法〖*2〗
1.传统动平衡识别方法回顾
机床主轴是典型的高速轴承-转子动力学系统,对于旋转设备而言,不平衡是导致其振动的主要因素。针对这一问题,1919年Jeffeott论述了进行动平衡的必要性,由此,转子动平衡技术在几十年历程中得到长足发展[8,9]。总体来说,经典的转子动平衡方法可基本归纳为两类:模态平衡法和影响系数法。
模态平衡法(modalbalancingmethod)利用了转子不平衡响应的模态特性,将不平衡量按各阶模态分解并予以平衡校正,从而抑制由振型失衡导致的振动。该方法基于两个重要假设:①转子系统阻尼足够小,以至于可以忽略;②各阶模态是平面、正交的。柔性转子的模态平衡法最早由德国的Federn于1956年提出,之后Bishop[10]、Gladwell[11]、Kellenberger[12]以及Saito[13]等从理论和实践两方面对该方法进行了深入、细致的研究,使之日趋成熟。
影响系数法(influencecoefficientbalancingmethod)与模态平衡法不同,它是一种实验方法,通过多次加试重运转,利用各测点的振动值求得影响系数,并基于该系数识别平衡校正量,平衡后可使选定的平衡转速下各测点的振动值降至所要求的程度。该方法由Thearle[14]于1934年首次提出,最初用于平衡刚性转子。1964年,Goodman[15]对影响系数法进行了全面的论述,首次给出了其通用表达式,引入了平衡方程的最小二乘解和加权最小二乘解,形成了实用的多平面、多转速的影响系数平衡法。1967~1972年,由Lund[16]、Tonneson[17]、Tessarzik[18]以及Little[19]等对这一方法进行了完善以及相关实验验证。
综合来说,上述两种方法各有利弊,利用模态平衡法进行高速平衡时,所需启动次数相对较少,且平衡高阶振型不影响低阶振型,但不平衡识别易受支承特性的影响,用于轴系平衡时不易获得单一振型,此外,要求平衡操作人员具备相关动力学知识,了解转子模态特性。采用影响系数法进行不平衡量识别时,可同时平衡多阶振型,用于轴系平衡更具优势,且不受支承特性的影响,易于利用计算机幅值实现,但高速下平衡时启动次数多,对高阶振型敏感性降低。为此,Drechsler[20]、Parkison[21]及Darlow[22]等提出了综合平衡的概念,即在影响系数法的基础上利用模态平衡法中的振型分离的特点选择平衡参数。该方法结合了二者的优点,但依然需要多次试车,若试重加载不当,反而会造成转子振动加剧,使动平衡操作复杂化。
2.动平衡识别方法研究进展与趋势
早期的学者专注于转子动平衡理论的研究,至20世纪80年代前后相关动平衡理论已经基本成熟。就转子动平衡基本理论本身来说,目前已经建立起以模态平衡法和影响系数法为基础的两大类平衡分析方法的完整理论体系。至今,种类繁多的平衡方法本质上基本仍分属于这两类平衡方法。这两类方法各有优缺点,在现场的应用中也都遇到一些问题,国内外学者开始尝试对上述平衡方法进行改进来提高平衡效率和精度。近年来相关的研究取得了大量的成果,主要有以下几方面。
1)考虑各向异性的平衡方法
大多数传统平衡方法基于各向同性假设,但是转子-轴承系统经过一段时间运行后,其轴承的刚度与阻尼一般都为各向异性[23],转子测量截面的单方向振动并不能精确地描述转子振动状态[7]。1965年Parkinson[24]研究了在各向异性轴承支承条件下的转子模态动平衡方法,但该方法在发生多阶模态振型混叠时误差较大。1979年Fujisawa等[25]指出受支承刚度各向异性的影响,对转子进行高精度动平衡时必须考虑转子进动的轴心轨迹。基于这一思路,工业现场开始采用双传感器垂直安装的方式来实现对每个转子测量截面振动信息的全面监测。1996年K
|
|